Pallet Rack for Freezers: Where to Start?
- Steve Freant
- Feb 28
- 3 min read
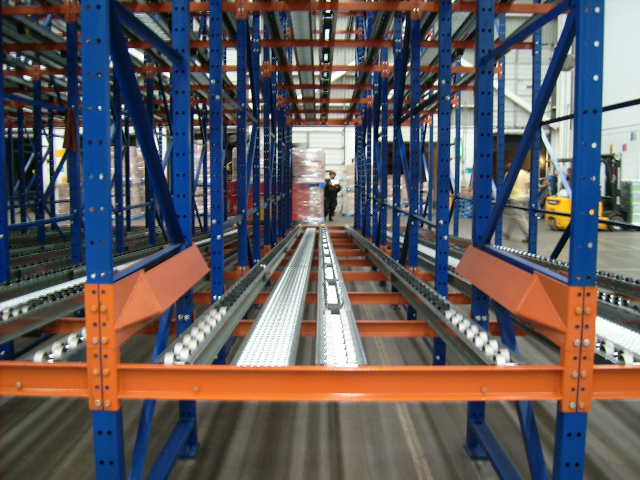
The demand for frozen ready meals, proteins, snacks, baked goods, fruits and vegetables, and desserts is soaring in the U.S. due to the convenience factor. According to a report from Research and Markets, the U.S. frozen food market was valued at $76 billion in 2023 and is expected to grow to $92.94 billion by 2029, reflecting a compound annual growth rate (CAGR) of 3.41%. As the market expands, the cold storage real estate sector is also experiencing growth. Colliers projects a 13.2% annual increase in this market through 2030, which will likely drive a corresponding rise in the demand for pallet rack systems designed for freezers.
Rack Configuration Optimizes Freezer Space Efficiency
Frozen foods typically require storage temperatures ranging from 10°F to -40°F. Due to the high cost of achieving and maintaining these low temperatures, facility owners often seek highly efficient, high-density storage solutions. The majority of the pallet rack systems we design for freezer environments are drive-in racks, as they effectively maximize storage density.
A denser rack system helps offset the storage space lost to wider travel aisles, which are necessary due to the visibility challenges forklift operators face when wearing heavy coats and protective gear. To mitigate the risk of rack impact, wider aisles are generally recommended, typically ranging from 10 to 12 feet, depending on the specifications of the forklifts in use.
The placement of building columns also plays a crucial role in freezer rack layout. Our rack engineers design systems that ideally place columns within or between the racking (a layout referred to as "buried"). When this is not feasible, the layout is adjusted to place columns in wider aisles, allowing for adequate forklift movement. Additionally, many freezer warehouses feature curbs along the perimeter walls and around building columns, which can affect the rack design. For this reason, it is highly recommended that a rack engineer conduct an on-site visit to assess the building's column layout, take precise measurements, and evaluate any other factors that may influence the design.
Guarding Protects Rack and Other Equipment

Most freezer warehouses utilize ammonia-based systems to generate sub-zero temperatures, with pipes and evaporators running near the ceiling to circulate ammonia throughout the freezer. This setup creates the required chill for the facility. Ammonia is toxic, so it is crucial to protect the ammonia lines from potential impact by a pallet load as an operator raises it overhead. Almost every freezer rack installation will include top ties at the top of the racks to prevent operators from lifting loads too high, given their restricted visibility. These top ties help safeguard the ammonia lines.
The steel used in freezer racking is typically more robust, as it must support significantly heavier loads. Pallets of frozen foods can weigh between 2,500 and 3,500 pounds, which generally requires 4-inch channel racks.
While freezer racks are inherently sturdy, they still benefit from additional protective measures to withstand impacts. The best practice is to install guards at the ends of exposed rack rows. It's also advisable to reinforce the front columns (aisle-facing) with an additional box channel on the upright, and to add angle deflectors. Additionally, using heavier beams and channel rub rails within the frame of a drive-in rack helps guide forklift operators when entering and exiting the structure, thereby reducing the risk of damage.
Special Considerations When Installing Pallet Rack Systems for Freezers

Building freezer warehouses is typically two to three times more expensive than constructing facilities for ambient temperatures. This increased cost is primarily due to the additional insulation, specialized freezer equipment required to maintain lower temperatures, and high-speed doors that open and close rapidly to preserve the cold air.
Moreover, the colder the freezer environment, the higher the installation costs. Installers must wear multiple layers of thermal protection, which can slow their work pace. Similar to the workers within the freezer, installers also need to take frequent breaks to warm up outside the cold environment. These factors both lengthen the installation process and raise overall costs.
Reach Out to EFS for Additional Best Practices
Want more information about rack designs for temperature-controlled areas? EFS offers several resources . Feel free to connect with our engineering team for additional insights, recommendations, and guidance.
Commentaires