Questions to Ask When Planning Your New Warehouse Solution
- EFS Engineering Group
- Sep 17, 2024
- 4 min read

When planning a new warehouse or distribution center, it’s essential to consider various factors, including designated storage areas and the methods for inventory management. For operations aiming to maximize the use of their building’s space, industrial steel storage racks offer an effective solution. These racks come in various styles and characteristics to suit different needs. To find the best option, it’s crucial to address four key rack specification questions when working with a manufacturer.
“A true warehouse design partner will identify and guide you through every step of the process to both keep you informed and build your knowledge base in effort to make everyone better,” says Steve Freant, President of EF Solutions Group. "There are a number of storage applications that may work but identifying which one would work best is nearly impossible without answering these basic questions. This will streamline any design process and create mutual buy in form all parties."

Question 1: What are the facility’s dimensions?
The dimensions of your facility are crucial when designing a storage rack system. “The first rack specification questions to consider should be the warehouse’s height and the square footage of its floor.,” says Freant.
"For instance, a facility with a ceiling height of 20 feet or less might be best suited for a static racking system (selective, pushback, etc.) In contrast, a warehouse with a much taller ceiling could accommodate an automated storage and retrieval system (AS/RS) with a stacker crane", he adds.
“In warehouses with limited floor space, achieving a cubing mentality is key, how much of the vertical space can we fill?,” Freant continues. “There are several systems that are designed to maximize unit load density but may not provide direct access to goods or select-ability.” Some of these high-density rack systems he was referencing include:
Drive-In/Drive-Through Racks: These systems allow for highly dense storage of multiple pallets of uniform products. Drive-in racks enable a forklift to enter from one side to pick up or deliver pallets resting on continuous rails. By eliminating multiple access aisles, drive-in racks can create additional pallet storage positions, making better use of the building’s footprint.
Pallet Flow Racks: Also known as Live Pallet or Gravity Flow racks, these systems are loaded from the back and provide first-in/first-out (FIFO) access. Pallets roll over gravity wheels or roller lanes, which are mounted at a slight downward slope from the loading point to the pick face.
Pushback Racks: These racks use nested carts that roll over inclined steel rails, typically holding two to six pallets per lane. Pallets are loaded from the front and pushed back by new loads, offering last-in/first-out (LIFO) access.
Pallet Shuttle Systems: These semi-automated systems enhance storage density and throughput by incorporating rails on which pallets rest. Motorized shuttles or carriers travel beneath the rails. The shuttle’s integrated platform lifts and transports the pallet back to the storage lane.

Question 2: What the specifications and/ or class of the stored inventory?
Understanding the characteristics of your inventory is crucial when selecting a storage rack system. Key factors include the dimensions (length, width, height), weight, and uniformity of the unit loads, which are essential for determining the most suitable type of rack.
“Inventory sizes can range significantly, from very small to very large. For the small loads, such as individual picks that are handled manually, metal shelving or carton flow racks are typically the most suitable options.” Freant says.
Alternatively, adjustable pallet racking systems with bins or panels may be recommended for organizing and storing individual cartons. For larger pallet loads, several types of industrial pallet racking systems are available, such as selective racks and the previously mentioned Drive-In/Drive-Through, Pallet Flow, Pushback, and Pallet Shuttle Systems.
In cases where the load is exceptionally long, such as tubes, beams, or pipes, cantilever racks are the most suitable. These racks are often used for storing oversized materials and are frequently employed in outdoor settings.
“It goes without saying that identifying the load dimensions is the single most crucial element when working with manufacturers to design solutions.” says Freant.

Question 3: How quick does the inventory turn?
The movement frequency of your inventory is another critical factor in selecting the appropriate rack system. Different products have varying turnover rates, which can influence the choice and installation of industrial racking.
Certain storage systems facilitate quicker stock rotation. FIFO pallet rack systems are ideal for inventory that needs to be dispatched promptly. However when the rotation is more flexible then LIFO based systems can be analyzed as well.
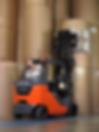
Question 4: How specific are the handling details of the inventory?
While many goods can be stored under standard ambient conditions, some products require specific environmental controls to prevent deterioration. This is often the case for food, beverages, or pharmaceuticals that need refrigerated or freezer storage.
Addressing any special handling requirements is essential. In cold storage or freezer environments, storage systems must support uniform temperatures and effective cold air circulation. Due to the high cost of maintaining cold temperatures, these warehouses typically use high-density, compact storage solutions. "This affords the client to maximize their cube in high cost square footage", Freant adds.
Additionally, if a facility stores hazardous materials, such as chemicals in liquid or powdered forms, it is important to inform the rack manufacturer about the chemical properties. This ensures that the racking system is compatible and helps prevent issues like corrosion or rust.

Our team is here for you!
If you require any assistance with designing your facility, we encourage you to reach out to the EFS team. Our experts are here to provide comprehensive support and guidance to ensure your design meets all your operational needs. Whether you need help with layout planning, selecting the right storage solutions, or integrating advanced systems into your facility, we are ready to offer personalized advice and solutions. Please do not hesitate to contact us; we are committed to helping you achieve the most efficient and effective design for your space. Your project will always be OUR PRIORITY!